Needles, cannulas, stylets, and other steel components are crucial to the performance and quality of many minimally invasive medical devices, including catheters. With all these components, there is a diverse range of design, manufacturing, quality, and performance options available.
We outline the main design considerations in this blog, starting with making sure needles, cannulas, and similar components are given enough attention during the early stages of the design process.
Consider Needles and Similar Components Early in the Design Process
Problems with needles, cannulas, stylets, and similar components are sometimes not discovered until a prototype for the device has been developed and functional tests are performed. One example is cutting performance, where it is discovered while testing a prototype that the cutting performance of the component is not sufficient for the intended use of the medical device.
Therefore, performance and design characteristics of needles and similar components should be factored into the design of the product in the earliest stages. This includes penetration force (see below), cutting performance, visibility, lubricity, and more. This helps prevent delays as the project progresses.
Point Geometries
Point geometries for needles are important to achieve the required level of sharpness as well as the necessary performance characteristics of the device. For example, a needle or cannula designed to penetrate veins or arteries will benefit from a different point geometry compared to a device designed to penetrate muscles or joint tissue.
Common point geometries for needle and cannula bevels include:
- Primary
- Menghini
- Madayag
- Pencil
- Trocar
- Lancet
- Chiba
- Franseen
- Spade
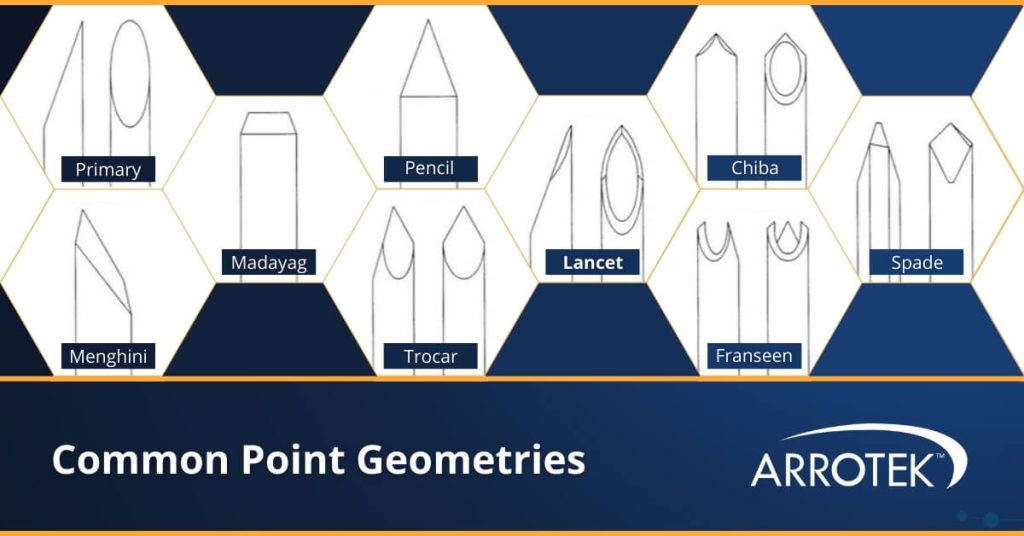
Balancing Performance Requirements
The process to design an advanced catheter or other minimally invasive medical device involves compromising on individual characteristics to achieve an overall level of performance. This applies to needles, cannulas, and other steel components of the device. As an example, we can use a minimally invasive medical device that performs a cutting action as part of the procedure.
Medical devices that perform a cutting action need to achieve the right balance between cutting force and tactile feel. Having to exert too much force to complete the required cut makes procedures riskier and more difficult to perform. The answer seems simple, i.e., sharpen the component as much as possible so a minimal amount of force is used. This can be achieved, for example, by changing the geometry of the component.
However, optimising the sharpness of the cutting component can have knock-on effects, including a loss of tactile feel during the procedure. Therefore, in this example, there needs to be a balance between sharpness optimisation and tactile feedback.
Quality Materials
It is important to specify the right quality, type, and grade of materials used to manufacture the needles and similar steel components in your medical device. Needles, for example, are typically 300-series or 400-series stainless steel.
Nitinol is also an option for specialist applications. Components made from nitinol benefit from enhanced elasticity and shape memory.
Manufacturing Techniques
The manufacturing techniques used to make needles and similar steel components will have a significant impact on the quality of the device. This includes manufacturing techniques used to create the sharp, leading, or cutting edge of the component. Examples include grinding, electrochemical cutting, and machining.
The availability of other manufacturing capabilities can also have an important impact on the design of needles and similar steel components in minimally invasive medical devices. An example is overmoulding, where two elements are overmoulded to create a single component. For example, a plastic component overmoulded onto a steel component. You can read more about the benefits of overmoulding for medical devices here.
Needle Size
Needles typically have a gauge size. For example, needles for FNA (fine needle aspiration) and FNB (fine needle biopsy) devices are typically between 22 and 25 gauge. The higher the number, the smaller the needle, i.e., a 25-gauge needle is smaller than a 22-gauge needle.
Coatings
Needles, cannulas, and similar steel components of minimally invasive medical devices can have coatings applied to enhance a required performance characteristic. For example, a PTFE coating can increase lubricity while other types of coating can give the component hydrophobic properties.
Coring vs Non-Coring Needles
The main difference in performance between coring and non-coring needles is that tiny pieces of skin and other materials can be withdrawn into the device with a coring needle. The design of a non-coring needle prevents this from happening.
Techniques to create non-coring needles include sandblasting the heel of the bevel to give it anti-coring properties. This is because the finish of the heel is often the main cause of coring. An alternative non-coring option is to make the bevel tip deflected or angled.
Other Design Considerations for Needles, Cannulas, and Similar Components
- Penetration force – determined by the point geometry of the needle, its sharpness, and the quality of manufacturing.
- Stylet – stylets are solid rods that are introduced into the needle. They are commonly used to prevent coring and to clear needles of occlusions.
- Echogenic markings – to increase the visibility of the device inside the body during the procedure.
- Luer and hub – fittings at the proximal end of a needle to connect another component such as a syringe.
- Lumen – the inside diameter of the needle or cannula.
- Bevel length – measured from the point of the needle to the end of the heel.
- Burr – the amount of deflection at the point of the needle. In most minimally invasive medical devices, any amount of burr above 0.001 isn’t acceptable.
Expertise at Arrotek
At Arrotek, we have extensive in-house expertise in all aspects of minimally invasive medical device design, including the design and specification of needles, cannulas, stylets, and similar components. We also have extensive manufacturing capabilities Centre of Excellence for Metals Manufacturing in North Attleboro, Massachusetts. To discuss your project or if you have a specific query, please get in touch and a member of our team will get back to you.