Overmoulding is a production technique used in the manufacture of medical devices. While it is a well-established technique, it has never been more important both in terms of manufacturing and the design of new medical device products.
With advanced overmoulding manufacturing methods, medical device product designers can push the boundaries of innovation to enhance existing products and create novel medical devices. This includes minimally invasive medical devices and, specifically, advanced catheter technologies.
What is Overmoulding
Overmoulding is an advanced form of injection moulding for specialist applications, making it an ideal solution in the medical device industry. It involves the full or partial moulding of one part over another to permanently join them together.
Overmoulding replaces the need to assemble the two parts downstream. For example, instead of gluing or welding the two parts together, they are manufactured as a single part.
Different materials can be used in the overmoulding process. At Arrotek, the catheters and other minimally invasive medical devices that we are involved with are made up of various polymers. As a result, we regularly use the overmoulding technique to permanently join two polymers together in our contract manufacturing work. We also take overmoulding into account as a design for manufacturing (DFM) consideration during the design process.
Two-Shot Overmoulding vs. Insert Moulding
There are two main types of process that come under the overmoulding umbrella – two-shot overmoulding and insert moulding.
Two-shot overmoulding involves two shots of injection moulding. The primary part geometry is moulded in the first shot with the second geometry then moulded with a different material in the second shot.
Insert moulding is an alternative overmoulding process where the first component is manufactured using a different process. This component is then overmoulded with a polymer or other type of material. The ability to utilize different manufacturing processes for the inserted components allows for a wide range of material flexibility and innovation. Metals, electrical components, and even other plastics can all be inserted and overmoulded with a compatible plastic material.
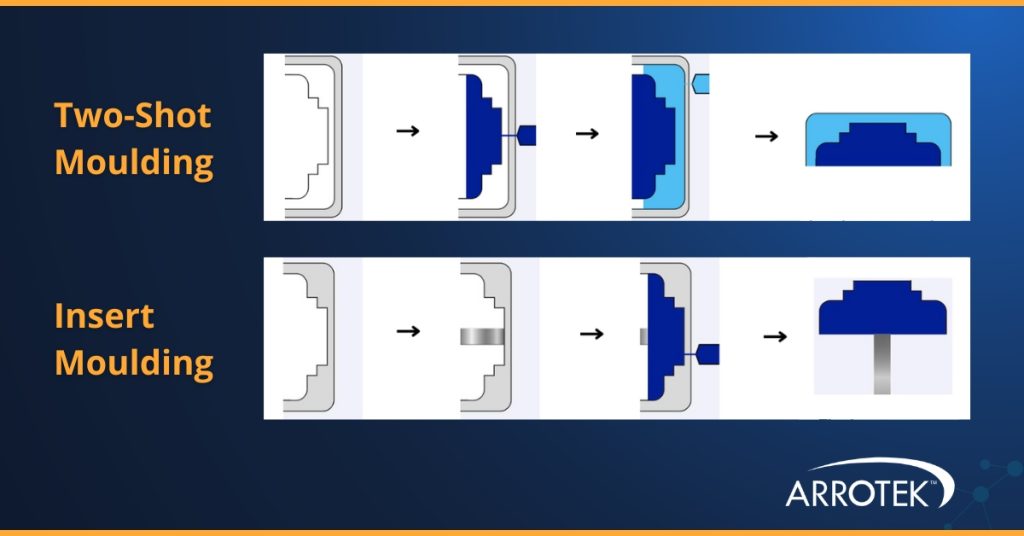
Benefits of Overmoulding for Minimally Invasive Medical Device Products
- Facilitates the use of smaller components in manufacturing, creating innovation opportunities during product design
- Improves adhesion between components
- Streamlines the manufacturing process by reducing individual components and downstream assembly operations
- Allows full or partial process automation
- Increases manufacturing throughput, helping to achieve production and cost targets
- Reduces waste, so saves money and helps medical device companies reduce their environmental footprint and reach their sustainability goals
- Improves the usability of the product which, in turn, can help reduce instances of incorrect product use, including incorrect use that leads to adverse incidents
- Reduces the number of individual components to improve the overall quality of the product, not least because variables in the manufacturing and assembly processes are reduced
- Enhances the aesthetic qualities of the product
Overmoulding is also an ideal solution for many production challenges that can exist with minimally invasive medical devices. In particular, by using overmoulding, you can save time in the design transfer stage as your design moves into production. This, in turn, reduces time to market for your new product.
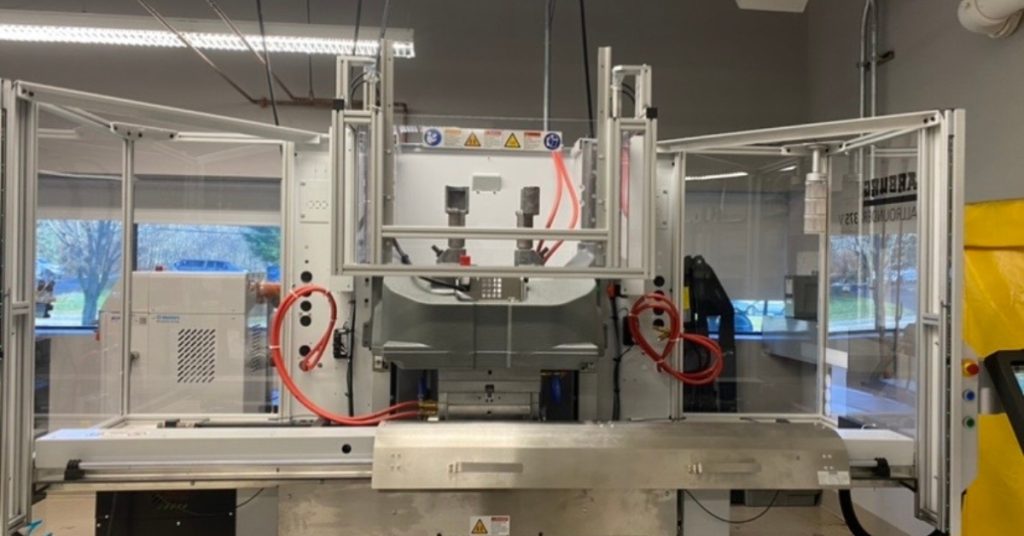
Product Design Benefits
The above list outlines the main overall business and production benefits of overmoulding. Overmoulding also offers product design advantages. In other words, overmoulding can enhance the performance of medical device products, particularly minimally invasive devices. The performance features that overmoulding can influence include:
- Abrasion resistance
- Waterproofing and sealing capabilities
- Strength and durability
- Biocompatibility
- Chemical resistance
- Electrical insulation
- Vibration resistance
- Grip and ergonomics
- Usability and safety, including the ability to add colours for safety and usability reasons
- Aesthetics
Overmoulding Design Considerations
There are essential considerations and challenges that must be taken into account when applying overmoulding either in the product design or design transfer process. For example, developing an overmoulding manufacturing process is complex and requires a high level of skill and precision.
There are also specific design considerations. The location of the gate/s is a good example. The gate is where the polymer is injected into the mould, so it’s important to carefully plan for its location in terms of manufacturability, product performance, product quality, and aesthetics.
Material selection is another design consideration example, as it requires knowledge of shrinkage rates, mechanical properties, and adhesion compatibility.
At Arrotek, we have the expertise to address these challenges and considerations both in our design and manufacturing teams. Whether you are looking for a contract manufacturer to meet your quality and production level targets, or a design partner that has a broad and deep range of knowledge across all aspects of the process, we can help. Get in touch and a member of our team will get back to you.