Design for Manufacture (DFM) involves designing products, including medical device products, so they can be efficiently manufactured. This includes ensuring the product can be manufactured within a target manufacturing cost while maintaining consistent quality, safety, and performance.
DFM also takes into account other factors that are crucial when designing minimally invasive medical device products, including regulatory compliance, usability, and the patient experience, but the realities of manufacturing the product remain a key focus.
The DFM process typically involves simplifying and refining the product at all stages in the design process with the aim of making it easier, faster, and less complicated to manufacture with as few steps in the manufacturing process as possible.
The number of parts used to manufacture a medical device product is also important. By going through a DFM process, design engineers will eliminate or combine parts to ensure there are as few as possible. This saves time in production and assembly, while the reduced number of steps to assemble the product (because there are fewer parts to assemble) reduces the risk of errors.
In addition to part reduction, parts standardisation is one of the main goals of DFM.
When Should DFM Begin?
By following a DFM process, problems that arise when designing and developing a new medical device product can be fixed during the design phase rather than later.
Therefore, it’s important to consider DFM principles during the early stages of the design process and then through each stage including concept development, CAD modeling, prototyping, and all design iterations.
It’s crucial to use DFM early in the design stage as the further into the process you go, the more costly it is to make changes.
For example, it is massively more expensive to make a change to the design of a product when you are at the mold designing and production stage compared to during the initial concept development, CAD modeling, and prototyping stages.
In other words, it’s important to ensure the product development specialist designing your new medical device product follows DFM principles.
What Does DFM Entail?
A DFM approach to designing a new medical device product involves questioning all aspects of the product and the design.
Doing this requires experience with similar products and designs. Knowledge of what others have done in the industry is also helpful, while a creative and innovative approach to MedTech product design is essential.
Factors Considered During a DFM Process
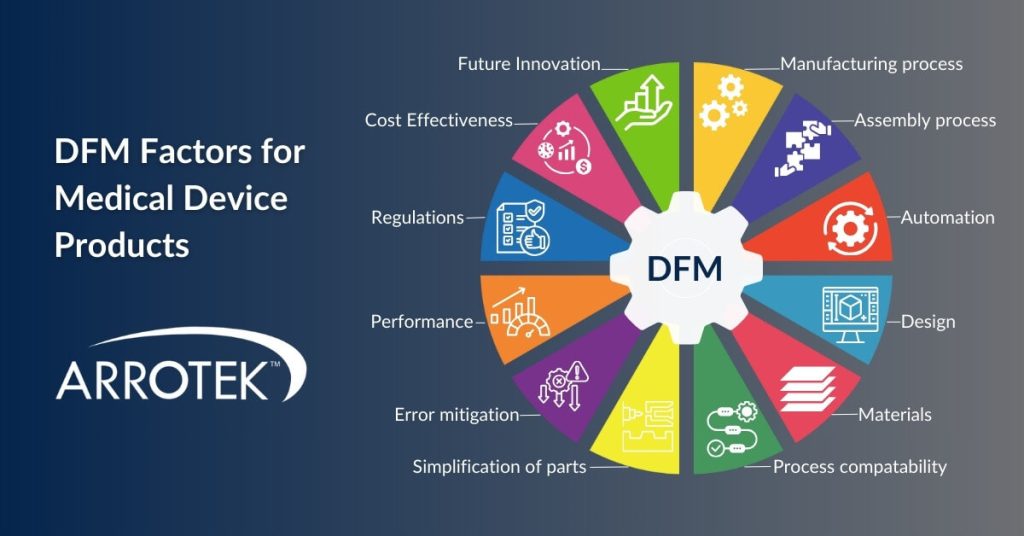
Manufacturing Process
This involves considering the method used to manufacture the product, i.e. machining, injection molding, 3D printing, etc. Consideration should be given to tolerances to ensure they are within an acceptable range for the chosen manufacturing process.
Assembly Process
Assembly is an important part of the overall production process, therefore assembly is also a DFM consideration. Sometimes this is referred to as DFA (design for assembly) or DFMA (design for manufacturing and assembly).
Similar principles apply when considering the assembly of a minimally invasive medical device product, i.e., minimizing the number of steps and components, reducing the potential for error, and making the assembly process as straightforward as possible.
Automation
Engineers will look at parts of the manufacturing and/or assembly process that can be automated. Adjustments to the design of the product can then be made to facilitate automated manufacturing.
Process Compatibility
DFM often takes into account the existing manufacturing capabilities of the facility that will be ultimately responsible for manufacturing the product. The aim is to minimise the need for new equipment or skills.
Design
The design of the new medical device product must adhere to Good Manufacturing Principles (GMP). For example, the design needs to consider the practicalities of manufacturing the components and then handling them for assembly. Does the design involve unnecessary steps that could be eliminated? The designer could also design the part so its production can be largely automated.
Materials
The materials that will be used to make the product are a crucial DFM consideration. In a minimally invasive medical device product, materials must be safe and biocompatible. Choosing the right materials also has an impact on the performance of the product as different materials and combinations of materials deliver different performance characteristics.
It is also important to consider the availability of materials in the supply chain, as well as purchasing costs and any impact the material will have on the manufacturing process.
Simplification of Parts
Key goals of the DFM process include:
- Minimizing the number of parts required to manufacture the product.
- Minimizing the complexity of parts and any other features that will make the medical device more difficult to manufacture and/or assemble.
- Avoiding the use of complex geometries or shapes in the product’s components.
- Avoiding the need for manufacturing or assembly processes that are labor-intensive or require specialist machinery.
- Using standardized components wherever possible.
Error Mitigation and Elimination
As part of DFM, engineers will consider the manufacturing process from start to finish to identify and assess the potential for errors. The focus will largely be on parts of the manufacturing and assembly process that have a human element. When a risk of human error is identified, engineers will consider what can be done to reduce or eliminate the risk.
Performance
The product should perform in real-world situations as expected and according to its defined functionality requirements. Therefore, the performance of the medical device should be a central consideration in the DFM process.
Regulations
The design of the product should also comply with all relevant regulations.
Cost Effectiveness
The cost of manufacturing the product is an important part of the DFM process. The aim is to ensure the cost of manufacture is aligned with the commercial strategy for the product without compromising on safety, quality, or compliance.
Future Innovation
Minimally invasive medical devices often go through multiple commercial release iterations as products are further developed and improved. DFM processes should take into account the potential for further development of the product.
Benefits of DFM
- Reduces the time it takes to bring a product to market
- Minimizes manufacturing transfer timescales and costs
- Reduces the overall cost of designing and developing the product
- Ensures the product can be made profitably
- Ensures a higher quality product
- Reduces the risk of production errors and product quality issues
DFM at Arrotek
As a full-service medical device design and manufacturing company, we have extensive experience in the DFM process at Arrotek. We have implemented DFM principles on minimally invasive medical devices at various stages of the design and development lifecycle. To find out more about DFM and how we can help with your project, please get in touch with us today.