Modern and innovative interventional and diagnostic catheters often have features, technologies, and performance characteristics that make them unique. There are, however, catheter design guidelines that apply in the vast majority of product development processes.
Points that are covered in the planning stage include, but are not limited to:
- Pre study
- Intended use/purpose
- User needs
- Functional requirements definition
- Device classification
These considerations feed into the design input requirements. They are needed to understand the scope of the product being developed so it can be properly planned.
We are focusing on the functional requirements for the purpose of this article. The design team will work to identify the key performance characteristics that will be required. Examples of those performance characteristics include:
- Wall thickness
- Diameter/French size
- Atraumatic access
- Lubricity
- Flexibility
- Kink resistance
- Push strength
- Torque transfer
- Tensile strength
Manufacturing, assembly, sterilization, and FDA regulatory considerations are also important. This means the design engineering processes DFM (design for manufacturing) and DFA (design for assembly) are also critical.
When considering the functional requirements, performance characteristics, and manufacturing/assembly practicalities, design engineers will typically take a layer-by-layer approach.
The Make-Up of Advanced Catheters
Advanced catheters come in a variety of forms, including single or multi-durometer, different wall thicknesses, and different methods of operation. They can also feature innovative technologies including sensors, electronics, fiber optics, and more.
Despite the variations that exist, the underlying architecture of most catheters involves three main layers:
- Inner layer
- Reinforcing layer in the middle
- Outer layer
It is beneficial to understand the broad catheter design guidelines for each layer.
Catheter Inner Layer Design Guidelines
We’ve already talked about the functional requirements and performance characteristics of the catheter device being designed. One of the most important factors in delivering on the functional requirements and achieving the performance characteristics is the material used in the design of the catheter’s inner layer.
From a design engineering point of view, the material selected for the inner layer impacts the design considerations and vice versa.
The main materials used in the design of catheter inner layers include:
- PTFE – polytetrafluoroethylene, a non-stick synthetic fluoropolymer.
- FEP – fluorinated ethylene propylene, a copolymer derived from fluoropolymer tetrafluoroethylene and fluoroalkene hexafluoropropylene.
- ETFE – ethylene tetrafluoroethylene, a fluorine-based plastic.
- HDPE – high-density polyethylene, a thermoplastic polymer.
- Polyamides – a class of copolymer known as a thermoplastic elastomer that is typically sold under the tradename PEBAX®.
Inner Layer Performance Characteristics
Each type of commonly used material for catheter inner layers offers different performance capabilities. The following is not an exhaustive guide but a high-level overview. Catheter design engineers will go into more detail based on the specific performance characteristics required for your device.
- PTFE offers excellent lubricity and the lowest coefficient of friction of any of the main materials used in modern catheter devices. It is also ideal for thin-wall designs and multi-durometer catheters.
- FEP offers good levels of lubricity and a low coefficient of friction, although not to the same standard as PTFE. It is more flexible than PTFE, however, and it is suitable for both single and multi-durometer designs.
- ETFE offers a mid-range level of lubricity compared to the other materials on this list. Where it stands out, however, is the high levels of tensile strength that it offers in addition to excellent impact resistance.
- HDPE offers good lubricity, albeit not to the same level as the previous materials highlighted in this list. It does, however, offer manufacturing and assembly benefits (see the next section).
- Polyamides are high strength making them ideal for many applications where the inner layer requires thin walls or must withstand high pressures.
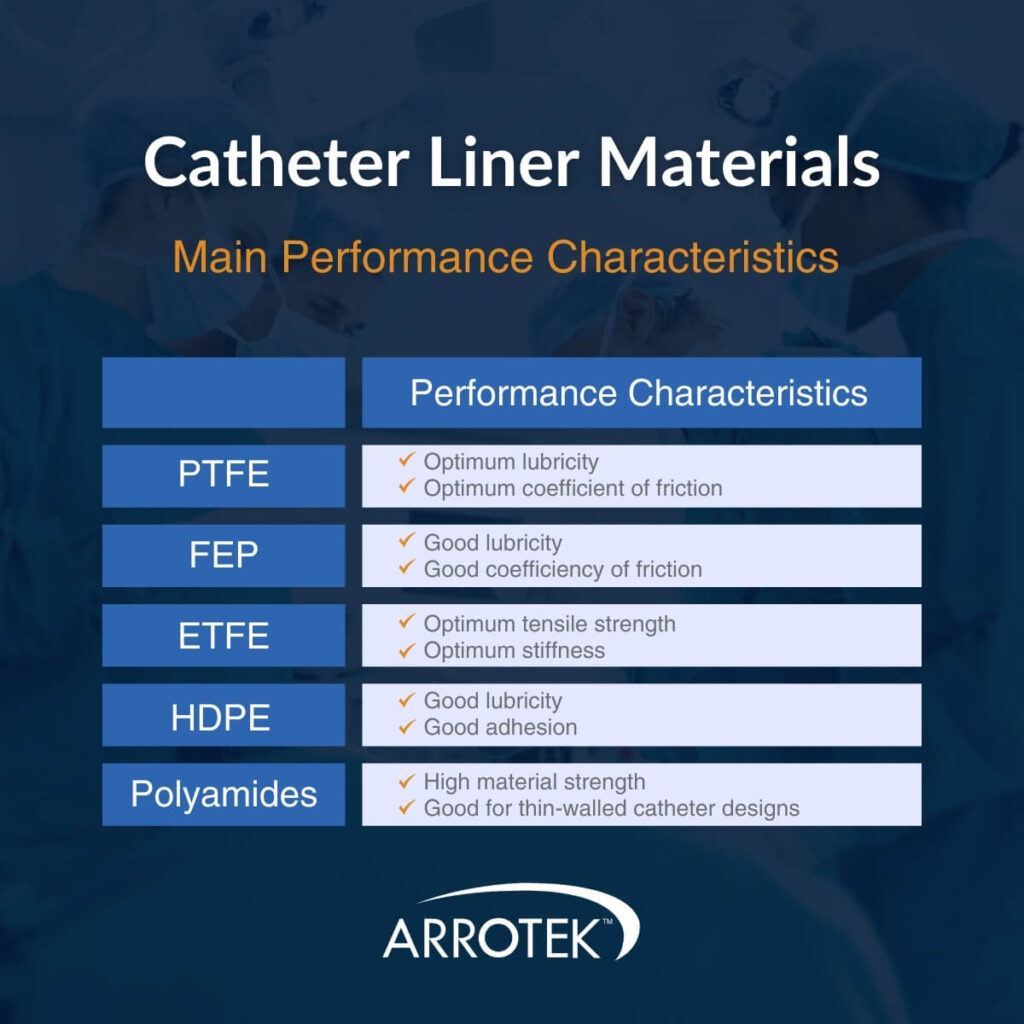
Inner Layer Manufacturing, Assembly, and Sterilization Considerations
Design engineering a new catheter device involves thinking about the production processes that will be required, including manufacturing, assembly, and sterilization. The key considerations include:
- Can a continuous manufacturing process using traditional methods of extrusion be used or will manual assembly be required?
- Is etching required to facilitate adhesion for the bonding together of the various components of the catheter?
- What type of sterilization processes are suitable?
In terms of sterilization, there are four main options:
- Gamma – sterilization using a gamma radiation source such as cobalt-60. The process takes several hours.
- EtO – sterilization using ethylene oxide gas. It is a popular method of sterilization in the medical device industry, not least because of its broad range of applications, but it takes several days to complete.
- E-beam – sterilization using electron beams. It is one of the fastest methods of sterilization.
- Autoclave – sterilization using high-pressure, high-temperature steam. The process typically takes less than an hour to complete.
Manufacturing, Assembly, and Sterilization Considerations by Inner Layer Material
- PTFE – typically requires manual assembly and etching as part of the production process. Suitable methods of sterilization are EtO and autoclave.
- FEP – single-durometer designs can be manufactured using a continuous process as well as some multi-durometer designs. Etching is required, however, a fact that will influence the manufacturing process. All methods of sterilization listed above – gamma, EtO, E-beam, and autoclave – are suitable.
- ETFE – single durometer designs can be manufactured using a continuous process, but etching is required. All methods of sterilization listed above are suitable.
- HDPE – continuous processes are often possible, especially with single durometer designs. Etching is not required. All methods of sterilization listed above are suitable.
- Polyamides – single-durometer designs can use a manual process. E-beam sterilization is not suitable but gamma, EtO, and autoclave can be used depending on other design features and characteristics of the device.
Catheter Reinforcing Layer Design Guidelines
The reinforcing layer is typically designed to increase the tensile yield of the catheter, i.e., to prevent the catheter from becoming deformed, especially in complex and tortuous vasculatures.
There are two main methods of reinforcing the central layer of a catheter:
- Braid reinforcement
- Coil reinforcement
It is also possible to use a combination of the two. Another common method of designing the reinforcing layer is to add variation along the shaft. For example, varying the pitch of the braid along the shaft.
Overview of Braid Reinforcement Design Guidelines
Engineers will design braid configurations (or braid patterns) to achieve the performance characteristics specified by the functional requirements.
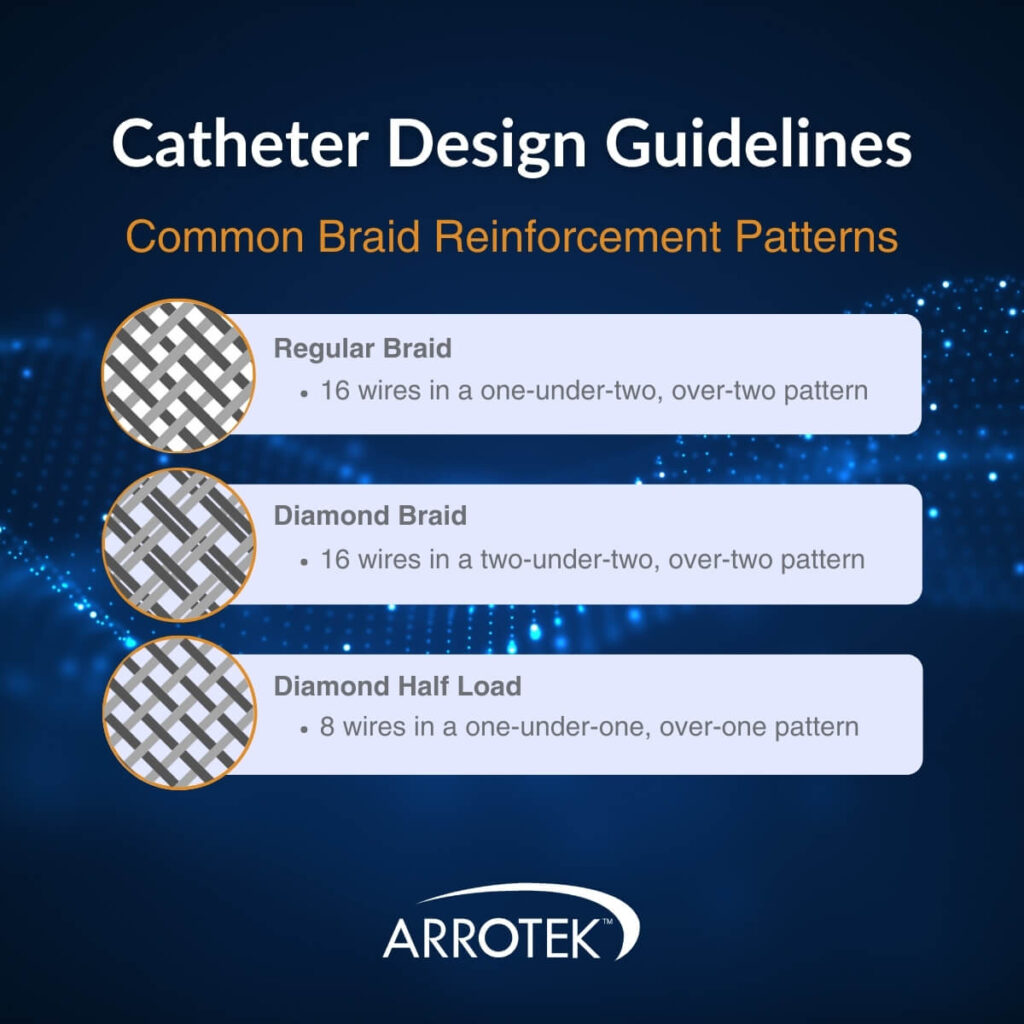
Two of the main performance characteristics that can be improved by braid reinforcement are torque control and push strength. Torque control effectively transmits the clinician’s twisting actions at the proximal end of the device to the distal end inside the patient’s body. Push strength helps the clinician pass the catheter through the vasculature, including when obstacles are encountered.
Overview of Coil Reinforcement Design Guidelines
Push strength is also a performance characteristic that can be achieved with coil reinforcement. Kink resistance and hoop strength can also be improved.
Catheter Outer Layer Design Guidelines
The outer layer of modern catheter devices can be designed using a range of biocompatible materials. One of the main considerations when designing the outer layer is preventing delamination between the outer and inner layers. The method of adhesion and the selection of materials are critical factors.
Custom Guidance and Tailored Advice
At Arrotek, we have extensive experience in catheter design projects. We work with start-up companies to develop novel and exciting product ideas, established medical device companies with new products to bring to market, and international corporations to augment in-house teams.
If you have a catheter design project, get in touch with us for custom guidance and tailored advice.